The Manufacturing industry is considered a cathedral of productivity and a source of enriched economy for any country. With metal 3D printing, it is expected shortly that this industry will flourish most of all sectors like food, plastic and architecture.
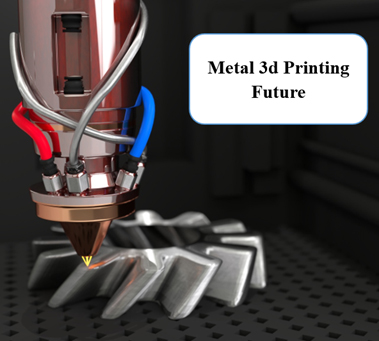
IDTechEX published a new report titled, “Metal 3D printing future: 2015 – 2025”. According to this report, explosive growth in metal additive manufacturing is expected within the said period.
Below are the key points mentioned in the report;
- Within the said period, we will slowly shift from plastic to metal 3D printing.
- The Metal additive manufacturing sector is a vast and most rapidly growing sector.
- With each year, printer’s sale is increasing by almost 48%.
- Material consumption is increasing by 32%.
- With the continuous increase in material consumption and printer sale, the highest chances of growth are possible.
- Since Production at earliest will be slow, that’s why industries that are suitable for additive manufacturing adoption are aerospace industry, biomedical industry and jewelry industry.
- Currently, metals being used in additive manufacturing are aluminum, cobalt, nickel alloys, titanium alloys, platinum and gold.
What is Metal 3D Printing
Additive manufacturing is a process of converting a digital file of product design into a three-dimensional object of a given material. It is considered opposite to subtractive manufacturing processes like machining and grinding.
The process of Additive manufacturing is divided into the following steps;
- Firstly, the 3D model is either downloaded from a directory or create using 3D cam software.
- Slicing software will be used to slice the software model into very small units or layers. This slicing layers will be fed into 3D printer devices using USB, or internet.
- Lastly, additive manufacturing of various types mentioned below is used to create a 3D solid object by following the slices layer by layer to achieve the required size and shape.
3D printing future technologies used for the metal industry are mentioned below;
- DMLM (Direct Metal Laser Melting)
The direct metal laser melting process is the most common additive manufacturing method used for tool steel like W1 tool steel, D2 steel, stainless surgical tool steels, etc. In this process, we have a fusion bed which contains powder of very small quantity. This small quantity powder will be melted according to slicing software giving a very thin layer of the sold part. With each layer solidifies, the thickness of part increases giving ultimately finished product.
- SLM/SLS (Selective Laser Melting or Selective Laser Sintering)
SLM and SLS are differentiated by the degree to which metal powder is melted. In SLS, partial melting of powder is taken place for fusing them in solid form, while complete melting in process of SLM is taken place. The term selective refers to the precise melting of building materials. It is suitable for porous structures where fusion is required in specific areas.
Sintering is a low-temperature process that makes SLS being employed low-temperature laser in contrast to high-temperature laser capable of melting for SLM. Dual component powders are employed in SLS and SLM. With laser of specific power, one form of powder gets melted while other form provides structural support and gives high porosity as well.
The metals which can processed using SLM are W1 tool steel, Maraging steel, Copper, and Aluminum.
The commonly employed metal powders in SLM processes are tungsten, W1 steel, D2 steel, Maraging steel Aluminum, and copper.
The SLM process uses atomized metallic powders, including titanium, tungsten, maraging steel, cobalt chrome, stainless steel, aluminum and copper.
- EBM (Electric Beam Melting)
This is considered as a rapid manufacturing process involves melting the metal powder layer by layer using an electron beam instead of laser in the presence of a vacuum.
3d Printing Future – Automotive Industry
The automotive industry is huge and always in front of adopting new technologies and advanced solutions to make manufacturing and assembling processes more sustainable. Metal 3D printing is being used in the Automotive industry far before it was adopted as an alternative to conventional manufacturing processes.
The most common application of Additive manufacturing is the development of prototypes of final products. Developments of products to estimate properties and finishing was time taking and costly. With additive manufacturing, prototyping is now smooth and simpler.
BMW’s Metal 3D Printing Applications
BMW is a brand known for its comfort and interiors. They are at the apex of experimenting additive manufacturing. Nowadays, lots of functional parts are being manufactured using additive manufacturing at additive manufacturing.
The most common application we have seen so far is the BMW i8 roadster folding roof mechanism. The brackets used for the folding roof are largely manufactured using 3D printing.
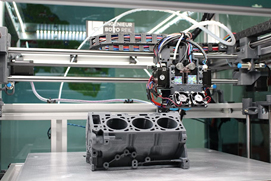
3D Auto vehicle cylinders being manufactured using additive manufacturing
Shelby Cobra 3D Printed Car
BAAM or big area additive manufacturing machine is widely used at Shelby cobra which utilizes 3D printers to develop and manufacture large size, strong lightweight composites for its latest auto model. This above mentioned 1400-pounds vehicle has 500 pounds of 3D printed parts containing almost 20% carbon nanofiber.

3D Printing Future – Tool Steel Industry
Tool steels are a type of alloy steel used for subtractive manufacturing. These tools are normally non-deformable and non-distorted nature used in a wide area of applications. In 2014, the tool manufacturing industry was estimated at around 82 billion dollars according to research firm Gardner Research. From that point, growth is almost 300% until today. The largest manufacturing units are in china producing 23.8 billion dollars’ worth of machine tools followed by Germany producing 12.9 billion dollars’ worth of respective steel alloy tools.
The tools like dies, cutting knives, blanking dies, brackets and many more are considered commodities for industry. They must be available at all cost. Without their presence, industry can not function. Tools manufacturing process is complex one involving casting, heat treatment, machining, heat treatment and coating respectively. All these processes come under top to bottom approach where initial billet is casted out of steel and then it is machined to desired shape after processing heat treatment.
With Additive manufacturing, it is possible now to build tools without any skilled labor and much of all complex manufacturing processes. In this process, most common tools used in industry has been started to manufacture as Additive manufactured W1 tool steel. W1 steel is common high carbon steel containing 90% martensite.
With w1 steel, commonly manufactured tools are Drift punches, forging dies, lathe center, knife and blades. For further information, follow W1 steel guide. Now, we can use additive manufacture such an important tool for industry using metal 3D printing.
3D Printing Future – Bio Printing
From 2006, Additive manufacturing research in the field of bio-industry started from tissue fabrication. In 2006, Cornell industry researchers had developed successfully, bio-inks with help of additive manufacturing. In 2012, tissue engineering started utilizing the concept of 3D printing to develop organs and body parts for academia and researchers.
In 2013, the Chinese started Additive manufacturing ears, livers, kidneys, and ears using specialized 3D printers. Now, titanium and stainless-steel implants are being developed at industrial for the biomechanics industry. Other than titanium implants, tools used in dental and surgical procedures are also begin developed using W1 tool steel and stainless steel.
Note – Choose the right printer for your home, office or business check out the detailed guide on thetechyboss a best review website about the tech stuff.